Like diving in a chocolate milkshake
November 25, 2015
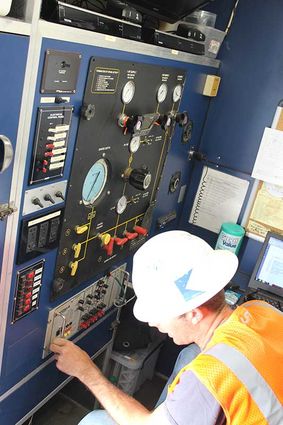
Keith Hanson
A team members keeps in communication with and monitors the air supply to the diver working at the weir in the Milk River.
The upgrade to the Water Treatment Plant in Chinook involves a lot of different skills and procedures to complete the project. A recent installation required calling in divers who specialize in underwater work. An air scour, a set of perforated tubes that uses air pressure to clean out river silt at the intake to the plant from the river, had to be replaced along with tubing that takes pressurized air to the cleaning device. The work had to be accomplished underwater adjacent to the weir across the Milk River.
The work was conducted by a dive team with Liquid Engineering Corporation, a Billings-based group that specializes in work with equipment related to handling and storing water. The company's divers do everything from inspections of the insides of water towers to maintenance and repairs of underground storage facilities. John Blankenship, Superintendent of the Water Treatment Plant, said divers with Liquid Engineering have done inspections and cleaned the large underground holding tanks currently used to handle water that is processed at the plant.
According to Blankenship, the old air scour was worn out and had to be replaced. He explained that the water intake is periodically cleaned out to assure an adequate flow of raw water from the river into the plant. To clean the silt and buildup at the intake an air compressor is attached to a two inch line that feeds to the air scour. The air scour's tubing is perforated and allows the pressurized air to escape and put the silt into motion. An eight inch water line, from the plant, is then opened to flush out the disturbed silt. The old scour had failed, allowing a lot of buildup.
The dive team consisted of four people. Only one diver at a time was able to work in the confined area around the intake. One team member would monitor the air pressure to the diver from a trailer some distance away. The diver had a direct airline plus a communication line and helmet mounted camera. The diver was always in communication with the person in the trailer. Other team members tended the diver, sending down tools or materials when the diver made a request through the communication system.
Blankenship said because of the failure of the old air scour there was a lot of material that first had to be shoveled out of the intake. Through a combination of hand shoveling and using a sludge pump the old scour was uncovered and removed. A new, stainless steel air scour was partially assembled on the bank of the river and then lowered to be installed. Holes had to be drilled, underwater, to attach the new scour to the weir that holds the water depth at the intake.
Because of turbidity in the river, all the work is basically done by feel as visibility is virtually zero. One diver described the experience as "about like diving in a chocolate milkshake." The diver's helmet-mounted camera was basically useless because of the low visibility.
The removal and installation took about two and a half days. Blankenship said that was a bit longer than anticipated, mainly because of low visibility in the river. He added, "Prior to starting the project the river had been fairly clear. About the time the divers came to do the installation the rains got everything all muddied and reduced visibility."
How are so many qualified divers recruited to a land-locked state like Montana? Jerod Birchell, at Liquid Engineering's headquarters, said the diving teams are all employees of the company, not contractors. Many of the divers come from Washington State. He said even a few divers are from other countries.
Birchell explained, "We hire a lot of ex-Navy divers and that explains how many of them came to Montana from the west coast."
He said during the summer months, when a lot of the company's work is done, the company has six teams with three divers on each team. In the winter, the number of teams drops to four. He said the company does projects in all fifty states throughout the year.
Liquid Engineering has a connection to the Hi-Line. Wayne Dykstra, the President of the company, was raised in Havre. He attended the University of Montana and served as a Naval Intelligence Officer during the Vietnam era. Dykstra is also the Managing Partner of ARC3 Corporation, a multi-national security consulting and tactical training firm involved with the homeland security mission.
The diving work is completed and the treatment plant can now be assured of a steady source of water from the Milk River. And any local who has observed the river after a heavy rain can appreciate the diver's description..."like diving in a chocolate milkshake."